Enhancing Productivity and High Quality Via Modern Metal Stamping Approaches
In the realm of manufacturing, the pursuit for boosted efficiency and top quality remains a perpetual objective. Modern steel marking methods have arised as a pivotal tool in accomplishing these purposes, transforming the market via a mix of advanced innovations and ingenious techniques. As the needs for precision and efficiency continue to intensify, the assimilation of automation and electronic devices into the steel marking process has actually come to be vital. However, the real procedure of success exists not only in the fostering of these modern-day strategies however also in the careful control of quality standards throughout the production cycle. By discovering the complex interplay in between technology, automation, and precision in steel stamping, a pathway towards exceptional productivity and high quality guarantee unravels.
Advantages of Modern Steel Marking
Modern metal stamping offers numerous advantages in regards to performance, accuracy, and cost-effectiveness in the manufacturing market. Among the essential advantages of contemporary metal stamping is its capacity to effectively generate high quantities of complex steel parts with consistent high quality. This procedure removes the demand for several operations as it can carry out different tasks such as blanking, puncturing, developing, and attracting in a solitary procedure.
In addition, modern metal marking enables suppliers to attain limited resistances and specific specifications, ensuring that each part fulfills the required requirements. This high degree of accuracy leads to minimal product waste, minimized rework, and overall better product top quality.
Additionally, modern metal stamping is a cost-effective production method. In essence, modern steel marking offers an affordable side to makers looking to improve efficiency and high quality in their procedures.
Advanced Technologies in Metal Stamping
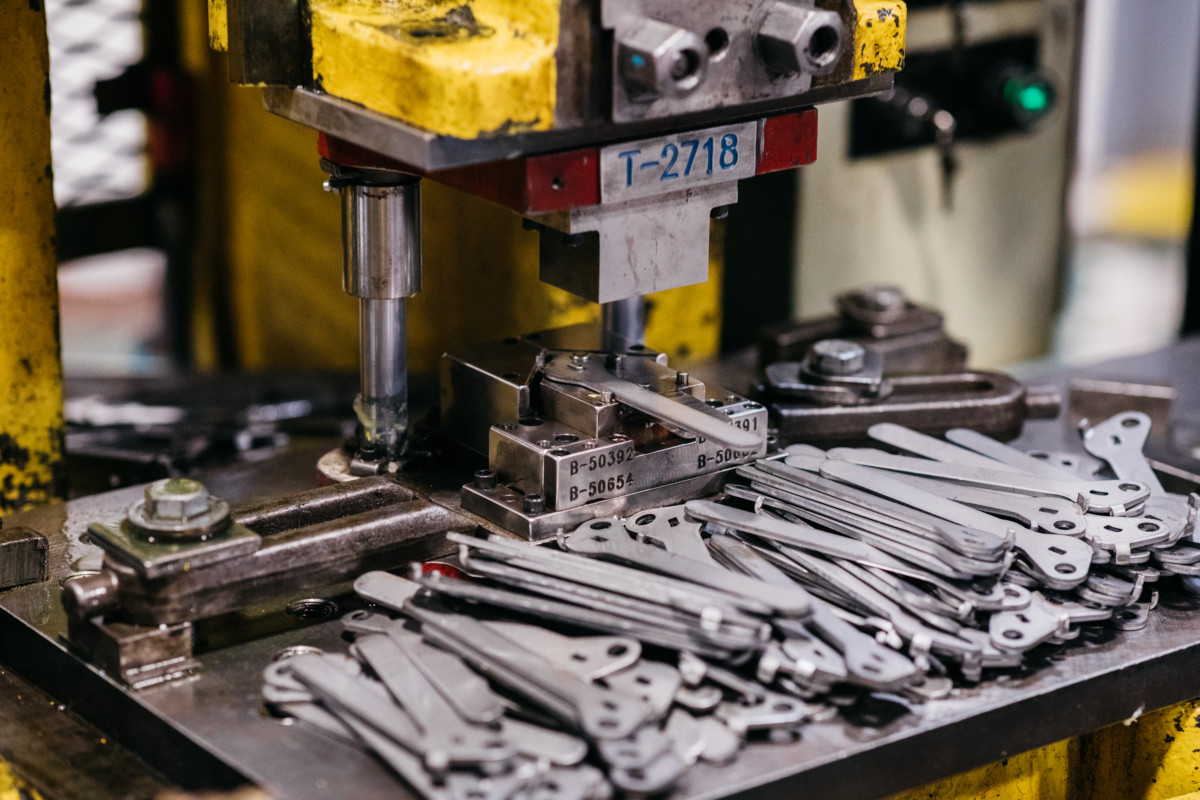
One more key innovation transforming steel marking is making use of servo presses. Unlike conventional mechanical presses, servo presses use greater control over the speed and force used throughout the stamping process. This control not only improves the top quality of the stamped components yet additionally reduces material waste and energy intake.
Furthermore, innovations in simulation software application have actually enabled suppliers to virtually test and optimize the marking procedure prior to physical production begins. This online prototyping aids identify prospective issues beforehand, bring about cost financial savings and faster time-to-market for brand-new products. Generally, these advanced modern technologies in metal stamping are driving extraordinary degrees of efficiency and high quality in the industry.
Improving Performance Via Automation
The integration of automated systems has actually substantially enhanced the performance of metal stamping procedures. Automation in steel marking operations offers a myriad of recommended you read advantages, consisting of boosted manufacturing rates, enhanced precision, and minimized labor prices. By utilizing robot arms and computer-controlled machinery, tasks that were formerly taxing and vulnerable to errors can now be performed swiftly and with impressive precision.
Automated systems have the ability to take care of recurring tasks with uniformity, resulting in higher productivity levels and lowered cycle times. This raised performance not just results in set you back financial savings however likewise makes certain a more structured and trusted manufacturing process. Furthermore, automation permits real-time tracking and information collection, enabling manufacturers to identify and address concerns without delay, more maximizing the general effectiveness of metal stamping procedures.
In addition, automation advertises a much safer working atmosphere by decreasing the need for hand-operated treatment in dangerous tasks. By delegating these duties to automated systems, employees can focus on more facility and value-added activities, adding to an extra reliable and effective process in the metal marking market.
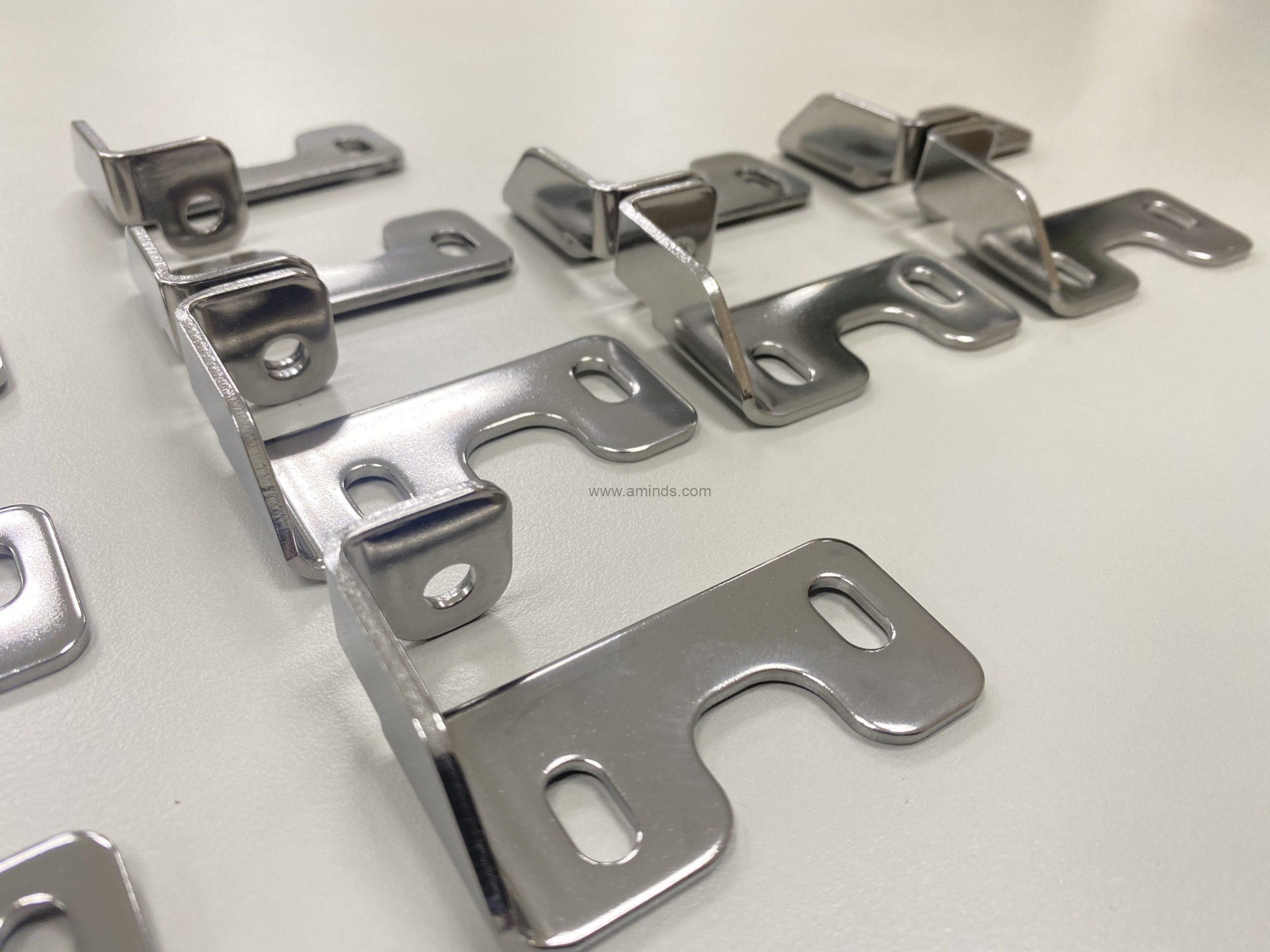
Quality Assurance Actions in Stamping
Executing stringent high quality control steps is paramount in making certain the precision and consistency of steel stamping procedures. By establishing durable quality assurance methods, makers can identify and remedy any inconsistencies or flaws in the stamped components, eventually boosting item high quality and customer contentment. One of the main quality control procedures in metal stamping is performing regular examinations throughout the production cycle. These assessments entail inspecting the measurements, surface finish, and general integrity of the stamped elements to validate compliance with the given needs.
In addition, implementing advanced innovations such as automated vision systems can additionally boost the top quality control process by enabling real-time tracking and discovery of any kind of abnormalities throughout production. These systems utilize video cameras and computer algorithms to examine get rid of high precision and accuracy, lessening the threat of issues running away right into the last item.
Additionally, establishing a comprehensive documentation system that videotapes quality assurance information and evaluation results is essential for tracking efficiency patterns and assisting in continuous improvement campaigns. By examining this information, makers can determine potential locations for optimization and carry out corrective activities to improve the overall top quality of their stamped products.
Enhancing Precision With Digital Devices
Utilizing electronic devices can considerably boost the precision of metal stamping processes, changing the method manufacturers attain accuracy in their manufacturing. Digital tools such as computer-aided layout (CAD) software application allow for the development of intricate marking designs with unbelievably accurate measurements. By inputting detailed specs into the software application, manufacturers can make sure that learn the facts here now each stamped item satisfies specific dimensional requirements, lowering errors and waste in the production procedure.
Additionally, the assimilation of sensors and real-time tracking systems in marking devices makes it possible for manufacturers to closely check the marking process and make immediate changes to ensure specific results. These digital tools give valuable information on variables such as pressure, speed, and placement, enabling quick recognition and improvement of any discrepancies from the wanted requirements.
Conclusion
In verdict, contemporary metal marking approaches provide various benefits for enhancing productivity and top quality in making procedures. These developments in metal marking not only streamline manufacturing procedures however also make certain regular useful site and top notch results - Metal Stamping.
Comments on “Metal Stamping Procedures: From Prototyping to Automation”